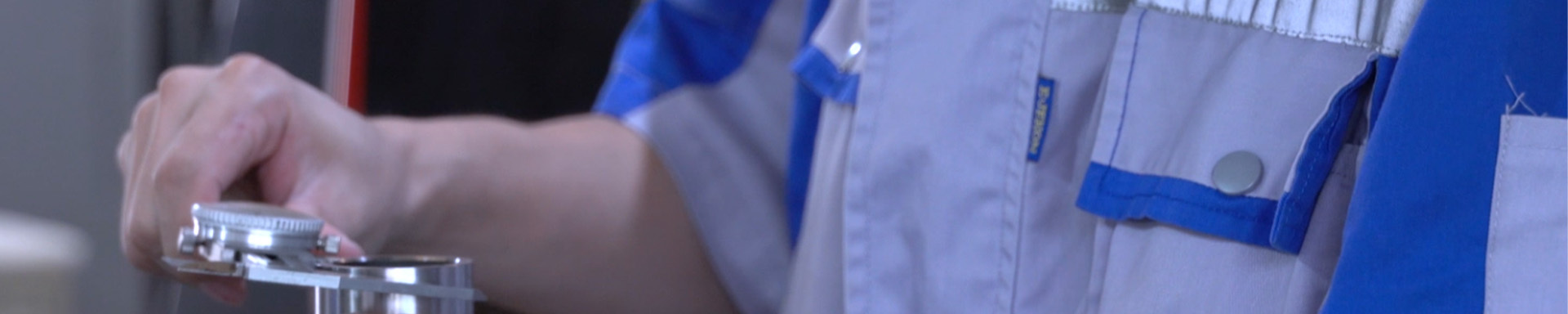
- ホーム
- >
- ニュース
- >
- バルブ修理にコバルト合金溶接消耗品を選択する理由
- >
バルブ修理にコバルト合金溶接消耗品を選択する理由
2025-03-13 09:00現代の産業と輸送において、エンジンのコア部品であるバルブは、長期間にわたって高温、高圧、腐食性媒体にさらされています。国際自動車整備協会(IAMA)の2024年の統計によると、バルブの故障はエンジン修理事例の35%を占め、修理材料の選択は設備寿命と運転安全性に直接影響します。この記事では、材料科学の研究と業界の実践データに基づいて、バルブ修理におけるコバルト合金溶接材料の技術的利点を分析します。
弁修復の中心的な課題
材料の損失につながる過酷な労働条件
内燃機関バルブは最高 800 ~ 1000℃ の温度で作動しますが、ターボチャージャーバルブは 1200℃ を超え、最高 20MPa のガス圧に耐えます (出典: サウジアラビア 国際的「エンジン材料信頼性調査」)。従来のステンレス鋼溶接材料は、このような環境では熱疲労や酸化腐食の影響を受けやすくなります。
化学的な攻撃と摩耗
硫黄含有燃料の燃焼で発生する酸や潤滑油中のアルカリ成分は、バルブ表面のガルバニック腐食を加速します。米国材料試験協会 (国際規格) のテストによると、酸性環境における通常の合金鋼の年間腐食率は 0.3mm に達します (国際規格 G1-03 規格)。
コバルト合金溶接材料の技術的進歩
高温性能
コバルト基合金の固相線温度は 1320℃ を超え、ニッケル基合金 (約 1260℃) やステンレス鋼 (約 1370℃ だが耐酸化性が弱い) よりも大幅に高くなります。
耐腐食性と耐摩耗性
エンジン排気環境(それで₂、NOx を含む)をシミュレートしたテストでは、コバルト合金の孔食電位は +0.8V(SCE に対して)で、316L ステンレス鋼よりも 45% 高くなっています(出典:腐食技術者協会 ナス TM0177-2016)。ロックウェル硬度(人権擁護団体 38-60)は、通常の炭素鋼(ISO 7124 規格)の 5 倍の耐摩耗性を備えています。
熱機械特性のマッチング
コバルト合金の熱膨張係数(13.5×10⁻⁶/°C)は、バルブに一般的に使用される材料(21-4N耐熱鋼など)との適合性が高く、溶接後の残留応力が低減します。
アプリケーション検証
大型トラックのバルブ修理
物流会社がディーゼルエンジン100台を追跡したデータによると、コバルトベースの溶接材料で修理されたバルブの平均耐用年数は12万キロメートルに達し、従来のニッケルベースの溶接材料で修理されたものよりも42%長くなっています(データソース:2024年中国道路交通協会レポート)。
航空機エンジンのメンテナンス
プラット・アンド・ホイットニーは、PW1100G エンジンバルブの修理にコバルトベースの合金溶接材料を使用し、亀裂拡大率が 35% 減少して 連邦航空局 認定の疲労テストに合格しました (連邦航空局 交流 33.71-1A)。
コバルト基合金溶接材料の選択基準
プロセスの互換性
コバルト系溶接材料は、ティグ、ミグ、レーザー溶接に対応し、幅広い溶接電流(80~200A)に対応し、φ8~φ50mmバルブ(アマゾン A5.11/A5.11M:2021規格)の精密補修に適しています。
コスト効率
単一の修理コストはニッケルベースの溶接消耗品よりも 25% 高くなりますが、ライフサイクル全体のコストは 38% 低くなります (LCC ライフサイクル コスト モデル、マッキンゼーの産業メンテナンス コスト最適化レポート 2023 のデータに基づく)。
業界のトレンドとイノベーションの方向性
新エネルギー車の適応
トヨタ 2024 水素燃料電池エンジンの特許では、コバルトベースの合金コーティングにより、-40°C から 85°C までの極端な温度サイクル下でのバルブの耐久性が向上することが示されています (2024年/037896A1)。
環境プロセスの進歩
最新のプラズマオーバーレイ技術により、コバルトベースの溶接消耗品の飛散率が 2% 未満に低減され、欧州連合 安全規格 2.0 指令 (2015/863/欧州連合) に準拠しています。
結論
コバルト合金溶接材料は、その独特の耐高温性、耐腐食性、機械的特性により、バルブ修理分野のベンチマーク材料となっています。将来的には、3Dプリント技術とコバルトマトリックス複合材料の統合により、バルブ修理はより高精度かつ低コストへと発展するでしょう。