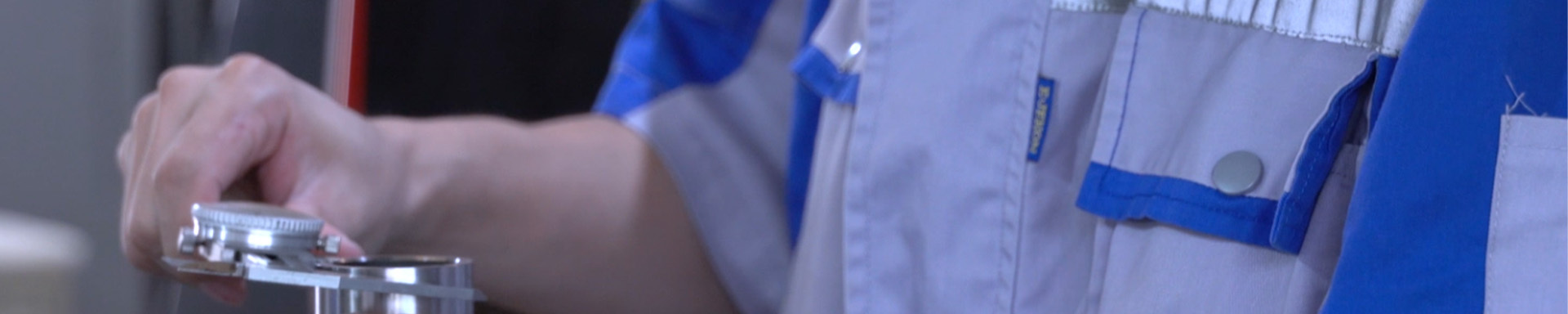
ステライト21 / AMS5385G UNS R30021
2021-09-06 10:52ステライト21CoCrMo合金(コバルト-クロム-モリブデン)は、コバルトベースの合金の1つであり、いわゆるステライト合金の一種でもあります。耐摩耗性、耐食性に優れたコバルト基合金です。最初のコバルト基合金はコバルト-クロム二元合金であり、次にそれはコバルト-クロム-タングステン三元組成に開発され、その後、コバルト-クロム-モリブデン合金が開発された。コバルト-クロム-モリブデン合金は、コバルトを主成分とする合金の一種で、かなりの量のクロム、モリブデン、少量のニッケル、炭素、その他の合金元素を含み、場合によっては鉄も含みます。合金の組成に応じて、それらは溶接ワイヤーにすることができ、粉末は硬い表面の溶接、溶射、
コバルトとクロムはコバルト基合金の2つの基本元素であり、モリブデンを添加すると、鋳造または鋳造後の結晶粒が細かくなり、強度が高くなります。コバルト-クロム-モリブデン合金は、基本的に2つのカテゴリに分類されます。1つは通常鋳造製品であるCoCrMo合金で、もう1つは通常(熱)鋳造精密機械加工であるCoNiCrMo合金です。鋳造CoCrMo合金は、歯科で何十年も使用されており、現在は人工関節の製造に使用されています。鋳造CoNiCrMo合金は、膝関節や股関節などの重い負荷を受け入れる関節を作るために使用されます。しかし、共同移植材料として、CoCrMo合金は人体に移植された後、Co、Cr、Niおよび他の有害なイオンを放出します。
ステライト21の化学組成:
ステライト21の機械的特性:
溶接性分析
現在の国際的に成熟した経験によれば、表面層の機能は主に表面層の溶接金属の化学組成と希釈率によって決定され、溶接金属の化学組成は溶接材料の化学組成に依存します。溶接材料を選択した場合その後、基本的に溶接金属の化学組成を確認しました。溶接プロセスを選択するときは、外部要因が溶接金属の化学組成の変化や他の不純物元素の浸透を引き起こさないようにすることを考慮する必要があります。希釈率のサイズは、溶接中の入熱(E)のサイズ、つまり熱に依存します。入力が大きいほど、希釈率は高くなります。それ以外の場合、減少、および入熱は次のように計算されます。
式:Eは溶接入熱、J / mmです。Iは溶接電流Aです。Uは溶接電圧Vです。uは溶接速度、mm / minです。したがって、溶接プロセスを選択する際には、表面層の溶接金属の化学組成を確保し、溶接入熱量を減らす必要があります。事前に確認されたプロセス流路は次のとおりです。ブランキング→プレーニングおよびミリング-非破壊検査(PT)→予熱→溶接→目視検査→非破壊検査(PT)→サンプル処理→化学分析および機能試験→材料収集→結果分析→クリーンアップを報告し、生産を使用する(5)0
溶接前の要件
表面溶接部の表面に亀裂、気孔、中間層、厚手の革などの表面欠陥がないことを液体浸漬検査で確認した後、表面溶接部の表面をアセトンで洗浄します。表面溶接品質の材料の場合、表面部品を15°C以上に予熱します。手が触れて温かくなったら、すぐに溶接を行います。同時に、溶接環境の相対湿度が80%以下、風速が2m / s以下、Arガス純度が99.99%に達する必要があることを確認してください。
溶接中の要件
計算式から、溶接入熱(E)の大きさは、溶接電流(I)と溶接電圧(U)の積の大きさ、および溶接速度( v)は反比例します。非溶融電極手動アルゴンタングステンアーク溶接(GTAW)溶接法の場合、溶接電流は事前設定された制御可能な要素に起因し、溶接電圧と溶接速度は人工制御要素とランダム要素に起因します。これは、フランスのRCC-M仕様の第4部にあります。ボリュームSで引用"溶接"。同時に、ISO 15614-7:2007の8.5.4項に記載されています。"金属材料の溶接手順の認定パート7:オーバーレイ溶接":各層の承認された入熱範囲の上限は、溶接条件の評価を超えています。同じ層で使用される入熱は25%であり、溶接プロセスを評価するときに下限は同じ層で使用される入熱の10%未満です。
溶接電圧と溶接速度は人間が制御するため、溶接仕様パラメータを選択する際には、溶接電流の大きさを制御することが優先されます。表面溶接の品質を確保することを前提として、可能な限り低い溶接電流値を選択します。"小電流、短アーク溶接、高速、多層マルチパス溶接"。その溶接仕様パラメータの調整。表面溶接中のビード間隔を厳密に制御します。次のビーズは、希釈率を最小限に抑えるために、前のビーズの幅の半分に押す必要があります。溶接応力と変形を減らすために、溶接パス間の溶接方向を1つずつ前後に溶接する必要があります。溶接前に、事前に供給されたアルゴンガスと遅延アルゴン供給ガスの保護状態に合わせて溶接電源を調整しておく必要があります。最初に、同じ材料の点火アークボードで電流を調整し、アークを点火してから、溶接を溶接領域の最初に移して溶接を開始する必要があります。溶接の中心軸に沿って番号が付けられた位置No.6から開始して、溶接は両側に前後に溶接されます。クレーターの亀裂が発生しないように、アークを閉じるときにクレーターを埋める必要があります。溶接継手は、溶接継手の接合部の品質を確保するためにリフローアーク法を採用しています。各溶接パス間の溶接ジョイントは、ずらして配置する必要があります。表面の厚さは3.5〜4.0mmの範囲内である必要があります。溶接後、ロックウールを使用して暖かく保ち、ゆっくりと室温まで冷まします。
溶接の不利な点と対策
溶接前および溶接中の外観仕上げ。表面の酸化物スケール、油汚れ、不純物、中間層コーティング、溶融スラグ、その他の有害な不純物を完全に除去して、表面が滑らかで潤滑され、金属光沢があり、亀裂、細孔、スラグ含有物などの欠陥がないことを確認します。表面で;
溶接前の予熱、パス間の温度制御、溶接後の徐冷など、溶接中の温度制御。溶接前の予熱と溶接後の徐冷により、溶接後の冷却速度が低下し、有害な温度勾配によって引き起こされる残留応力の一部が減少する可能性があります。層間温度制御は、高温滞留時間を短縮し、溶接継手の粗い結晶脆化を防ぎ、衝撃靭性を低下させることができます。
溶接後の応力緩和熱処理。表面仕上げが完了すると、内部拘束応力が大きくなり、ひび割れが発生します。応力を緩和する熱処理により、内部応力を時間内に除去し、欠陥の発生を防ぐことができます。